Why Do Blades Warp When Quenched?-Understanding the Phenomenon
The intriguing phenomenon of blade warping during the quenching process. This enigma arises from the intricate interplay of metallurgical transformations and the rapid cooling inherent to heat treatment.
Blades, meticulously crafted with precision, can unpredictably distort, challenging artisans and metallurgists alike.
Understanding the underlying factors behind this occurrence is essential for producing high-quality, reliable tools. Uneven temperature distribution, quenching medium selection, and material composition all play pivotal roles.
Mastery of these nuances empowers bladesmiths to navigate the fine line between achieving optimal hardness and minimizing structural distortions.
Delving into the science of quenching unveils a captivating journey into the heart of metallurgy and craftsmanship.
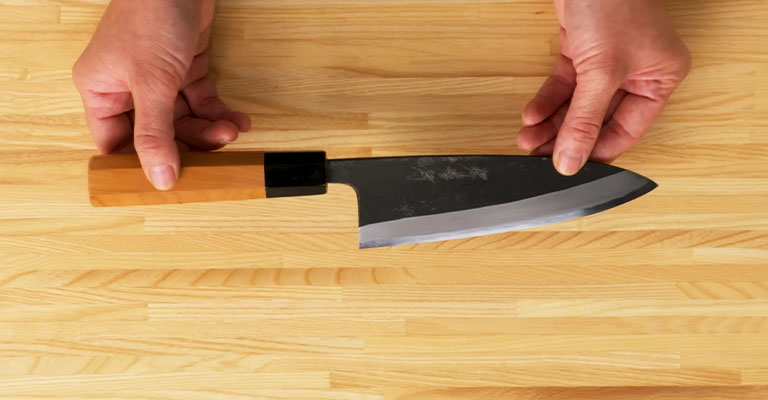
Why Do Blades Warp When Quenched?
Blades can warp during the quenching process for several reasons, which primarily stem from the rapid and uneven cooling that occurs when hot steel is immersed in a quenching medium (typically oil, water, or air).
Here are the main reasons why blades may warp during quenching:
Temperature Differential
Blades are often complex in shape, with varying thicknesses along their length. Thicker sections, like the spine, retain heat longer than the thinner cutting edge.
During quenching, this temperature discrepancy causes uneven contraction, leading to warping. Bladesmiths must carefully monitor and manage the heating process to ensure uniform temperatures across the entire blade.
Uneven Heat Distribution
Achieving uniform heat distribution throughout a blade is crucial. Variations in temperature can occur due to inconsistencies in the heating process.
For example, localized hot spots can develop if the blade isn’t evenly heated in the forge. These hot spots lead to uneven cooling rates during quenching, ultimately resulting in warping.
Internal Stresses
The forging process subjects the steel to significant shaping and manipulation. This can create internal stresses within the blade’s structure.
When the blade is quenched, these stresses can be either released or exacerbated, causing deformation. Properly conducted normalization and stress-relief processes before quenching can help mitigate this issue.
Quenching Medium
The choice of quenching medium is critical. Different mediums provide varying rates of cooling. For instance, water cools steel rapidly, while oil offers a slower, more controlled cooling rate.
Using the wrong quenching medium for a specific type of steel or blade design can result in uneven cooling and subsequent warping.
Inadequate Preheat Treatment
Preheating prepares the blade for quenching by ensuring it reaches an even, appropriate temperature.
When this step is rushed or not executed properly, the blade may not heat uniformly. Consequently, rapid quenching can lead to thermal shock, causing warping.
Improper Quenching Technique
The actual quenching process demands precision. Blades should be fully immersed and held vertically to ensure even cooling.
An angled or uneven immersion can result in uneven cooling rates and subsequently, warping. Skill and experience are crucial in executing this step accurately.
Material Composition
Different steel alloys have unique heat treatment requirements. Using steel that doesn’t match the intended use or neglecting specific heat treatment protocols can lead to suboptimal outcomes.
Bladesmiths must be well-versed in the properties of their chosen steel to avoid potential warping issues.
Cooling Rate Control
Techniques like differential or selective hardening are advanced methods used to enhance a blade’s performance. These methods intentionally cool different parts of the blade at different rates.
While this can provide benefits, it requires precise control and expertise. Mishandling this process can result in unintended warping.
Post-Quenching Manipulation
Immediately after quenching, the blade is extremely hot and malleable. Handling or attempting to work on it during this phase can introduce additional stresses.
Bladesmiths must exercise patience and allow the blade to cool sufficiently before any further manipulations.
Inadequate Annealing
Proper annealing after forging is crucial to relieve any residual stresses from the shaping process.
When this step is overlooked or not executed effectively, the blade may retain internal stresses that increase the likelihood of warping during quenching.
Metallurgical Changes During Quenching
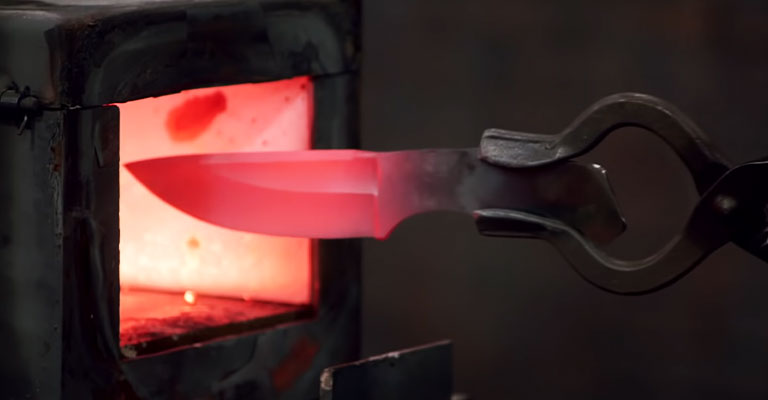
During the quenching process, several important metallurgical changes occur in the steel. These changes are crucial for achieving the desired mechanical properties in the final product.
Here are the key metallurgical transformations that take place during quenching:
Austenite to Martensite Transformation
At high temperatures, steel is in its austenitic phase, which has a face-centered cubic (FCC) crystal structure.
As the steel is heated and then rapidly cooled during quenching, it bypasses the normal phase transformation to pearlite or other phases. Instead, it undergoes a diffusionless transformation known as martensitic transformation.
Rapid Cooling Rates
The speed at which the steel is cooled during quenching is critical. Rapid cooling rates are necessary to achieve a fully martensitic microstructure.
Slow cooling allows time for other phases, like pearlite or bainite, to form, which would reduce hardness.
Residual Stresses
The rapid and uneven cooling during quenching introduces significant internal stresses in the steel.
These stresses are a result of the non-uniform volume change associated with the martensitic transformation. Proper tempering after quenching helps relieve some of these residual stresses.
Hardness and Brittleness
Martensite is very hard but also very brittle. While this hardness is desirable for cutting tools and certain applications, it can make the steel susceptible to cracking or fracturing under high impact or stress.
Tempering is often used to reduce brittleness while maintaining a high level of hardness.
Quench Severity
The severity of the quenching process, which is determined by factors like the quenching medium and its temperature, significantly influences the resulting microstructure and hardness of the steel.
For instance, water quenching cools the steel more rapidly compared to oil, resulting in a harder but potentially more brittle material.
Transformation Kinetics
The kinetics of phase transformation during quenching depend on factors such as the alloy composition, grain size, and cooling rate.
These factors can influence the extent and nature of the transformations, ultimately affecting the final properties of the steel.
Retained Austenite
In some cases, a small amount of austenite may remain in the steel after quenching. This can be undesirable as it can reduce hardness and stability.
Subsequent tempering is often used to transform any remaining austenite to a more desirable phase.
Microstructure Variation
The microstructure of the steel after quenching is highly dependent on factors like composition, initial grain size, and cooling rate.
Different microstructures, such as lath martensite, plate martensite, or retained austenite, can have varying effects on the final properties of the steel.
The Quenching Process
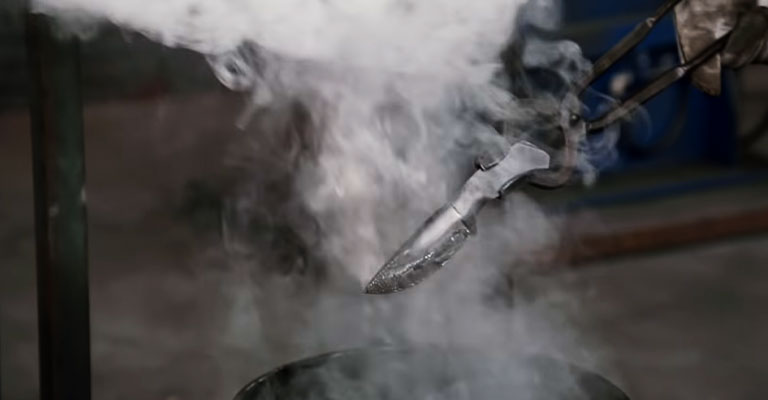
The quenching process is a critical step in the heat treatment of steel, playing a pivotal role in determining its final mechanical properties. It involves rapidly cooling a heated steel component in a controlled manner.
Here’s a detailed overview of the quenching process:
Heating
Before quenching, the steel component is heated to a specific temperature. This temperature, known as the critical temperature, varies depending on the type of steel and its intended application.
For most carbon steels, the critical temperature is typically between 700°C to 900°C (1292°F to 1652°F).
Critical Temperature and Phase Transformation
At the critical temperature, the crystal structure of the steel changes.
The steel transitions from its original phase, which is typically ferrite and pearlite for low-carbon steels, to an austenitic phase with a face-centered cubic (FCC) crystal structure.
This phase change is essential for the subsequent quenching process.
Rapid Cooling
Quenching involves rapidly and uniformly cooling the heated steel. The speed at which the steel is cooled is critical for achieving the desired microstructure and mechanical properties.
This rapid cooling is necessary to bypass the normal phase transformations and promote the formation of martensite.
Quenching Medium
The choice of quenching medium plays a crucial role in the process. Common quenching mediums include water, oil, and air. Each medium offers different cooling rates.
Water provides the most rapid cooling, followed by oil, and then air. The selection of a quenching medium depends on factors such as the steel type, component geometry, and desired final properties.
Microstructure Transformation
As the steel rapidly cools, it undergoes a diffusionless transformation known as the martensitic transformation.
This transforms the steel’s crystal structure from austenite to martensite, characterized by a body-centered tetragonal (BCT) structure. Martensite is known for its high hardness and strength but is also brittle.
Residual Stresses
The rapid and uneven cooling during quenching introduces significant internal stresses in the steel.
These stresses are a result of the non-uniform volume change associated with the martensitic transformation.
Post-Quenching Processing
After quenching, additional steps are often necessary to achieve the desired properties. One crucial post-quenching step is tempering, which involves reheating the steel to a specific temperature and then cooling it at a controlled rate.
Tempering helps reduce the brittleness of martensite while maintaining a high level of hardness.
Inspection and Quality Control
Finally, the quenched and tempered steel component is inspected for any defects or deviations from the desired specifications. This may include checking for hardness, straightness, and other quality parameters.
Techniques to Minimize Warping

Minimizing warping during the heat treatment process is a crucial aspect of producing high-quality steel components.
Here are some techniques that can help reduce the likelihood of warping:
Pre-Heating and Soaking
Ensure the steel is uniformly pre-heated before reaching the critical temperature. This promotes even heating and reduces temperature differentials within the material.
Allow the steel to soak at the target temperature for sufficient time to ensure uniformity.
Even Heating and Heat Distribution
Use a well-calibrated and evenly distributed heat source, such as a furnace or a forge, to ensure uniform heating across the entire workpiece.
Avoid localized hot spots or cold spots that can lead to uneven thermal expansion.
Proper Quenching Medium Selection
Choose the appropriate quenching medium for the specific type of steel and application. Water provides rapid cooling, while oil offers a slower, controlled rate.
Air quenching is the slowest method. Selecting the right medium helps manage the cooling rate effectively.
Quench Tank Design
Ensure the quench tank is large enough to allow for uniform immersion of the workpiece.
The tank should have sufficient capacity to avoid crowding, which can lead to uneven cooling.
Vertical Quenching
When quenching blades or similar components, ensure they are held vertically to promote even cooling.
This reduces the likelihood of warping due to uneven cooling on different sides of the blade.
Avoid Sudden Movements After Quenching
After quenching, avoid any sudden or forceful movements that may introduce additional stresses. Allow the workpiece to cool and stabilize before further handling.
Tempering
After quenching, tempering is a crucial step to relieve internal stresses and reduce brittleness while maintaining hardness. Proper tempering can help minimize the risk of warping.
Straightening During Tempering
When warping occurs during quenching, it can often be corrected during the tempering process.
Carefully straighten the workpiece while it’s at the tempering temperature, taking care not to overdo it, as excessive bending can introduce new stresses.
Use Jigs and Fixtures
Employing jigs and fixtures designed to hold the workpiece in the desired shape can help prevent distortion during heating and quenching.
Proper Annealing
Ensure that the steel undergoes proper annealing before the quenching process. This helps to relieve internal stresses from prior processing steps, reducing the likelihood of warping.
Minimize Overheating
Avoid excessive heating beyond the critical temperature. Overheating can lead to grain growth and other structural irregularities, increasing the risk of warping.
Quality Control and Inspection
Regularly inspect the workpieces for any signs of warping or distortion throughout the heat treatment process. Early detection allows for timely adjustments.
Common Mistakes and Misconceptions
In the field of metallurgy and heat treatment, there are several common mistakes and misconceptions that can lead to suboptimal results or even failure in achieving desired material properties.
Here are some of the most prevalent:
Insufficient Preheating
- Mistake: Failing to adequately preheat the steel before reaching the critical temperature.
- Consequence: Inadequate preheating can lead to uneven heating, resulting in variations in material properties and an increased risk of warping.
Improper Quenching Medium Selection
- Mistake: Choosing the wrong quenching medium for a specific type of steel or application.
- Consequence: Using an inappropriate quenching medium can lead to uneven cooling, affecting the final hardness and mechanical properties of the steel.
Neglecting Tempering
- Mistake: Skipping or not properly performing the tempering process after quenching.
- Consequence: Failure to temper can result in excessively brittle steel, leading to increased risk of fracture and reduced overall toughness.
Overheating
- Mistake: Allowing the steel to reach temperatures significantly higher than the critical temperature.
- Consequence: Overheating can cause grain growth, resulting in coarse microstructures and reduced mechanical properties.
Insufficient Quenching Time
- Mistake: Removing the steel from the quenching medium prematurely.
- Consequence: Insufficient quenching time can lead to incomplete martensite formation, resulting in reduced hardness and strength.
Rapid Quenching without Prior Normalization
- Mistake: Quenching without first normalizing the steel.
- Consequence: Skipping normalization can lead to residual stresses and uneven microstructures, increasing the risk of warping and structural irregularities.
Ignoring Grain Size Considerations
- Mistake: Neglecting the influence of grain size on the final properties of the steel.
- Consequence: Larger grain sizes can lead to reduced toughness and ductility, affecting the overall performance of the material.
FAQs
What Causes Blades to Warp During Quenching?
Uneven cooling rates and internal stresses induced by the rapid quenching process can lead to warping in blades.
Can Proper Preheating Prevent Blade Warping?
Yes, ensuring even preheating of the blade helps minimize temperature differentials, reducing the risk of warping during quenching.
Is Quench Severity a Factor in Blade Warping?
Yes, the choice of quenching medium and its temperature significantly influences the cooling rate, which in turn affects the likelihood of warping.
Do Different Steel Types Respond Differently to Quenching?
Yes, different steel alloys have unique compositions and heat treatment requirements.
Can Tempering Help Reduce Blade Warping?
Yes, tempering helps relieve internal stresses introduced during quenching, reducing the risk of warping while maintaining desirable hardness levels.
To Recap
The phenomenon of blades warping during the quenching process is a result of several intricate factors. Uneven cooling rates, internal stresses, and the selection of quenching mediums are critical contributors to this occurrence.
Understanding the precise requirements of the steel being used, ensuring proper preheating, and carefully managing the quenching process can mitigate the risk of warping.
Achieving the right balance between hardness and toughness while preventing structural deformities is a skill that bladesmiths and metallurgists continually hone.
By employing best practices and maintaining a deep understanding of the metallurgical changes during quenching, bladesmiths can produce blades of exceptional quality, free from warping defects.